Australia’s housing construction costs have cooled from pandemic peaks but modular construction offers 10-20 per cent cost savings and 50 per cent faster build times to address affordability.
Last week, the Reserve Bank kept interest rates on hold, in part due to ongoing concern about the cost of housing construction. While national construction costs have cooled from their pandemic peaks, dropping from 17.8 per cent annual growth in December 2022 to 1.4 per cent in March 2025 -the damage to housing affordability has been severe.
Western Australia exemplifies the ongoing challenges, with construction costs still rising at 10.7 per cent annually. Even markets showing declines like NSW and Victoria are building from a dramatically higher base. This cost inflation has fundamentally altered housing construction economics, making traditional building methods increasingly unviable for affordable housing.
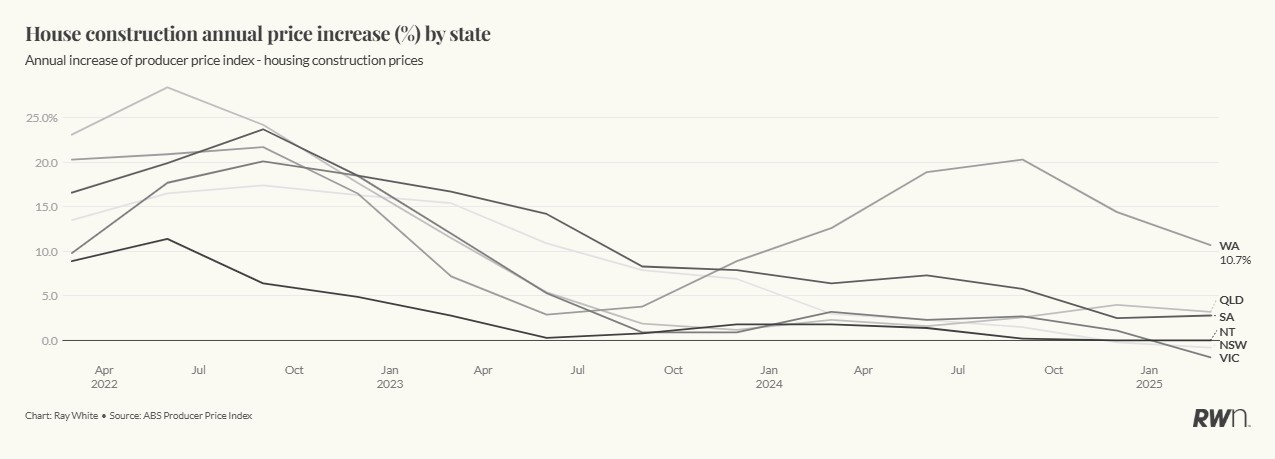
A major challenge in reducing costs is that Australia’s housing construction industry has remained largely unchanged for decades, relying on site construction that is inherently inefficient. The traditional process requires coordinating multiple sub-contractors across numerous sites with varying conditions and logistical challenges.
It has been further compounded by labour shortages. Master Builders Australia research has found that the industry requires 90,000 new workers to meet current demand – a shortage that would require 360,000 years of training if filled entirely through traditional apprenticeships.
Rising costs, inefficiencies in the way homes are built and labour shortages has meant that dwelling completion times have now reached historic highs. The average house now takes over 10 months to complete, compared to 6-7 months in normal conditions. Against this background, modular construction is now emerging as a way to increase efficiency in housing construction.
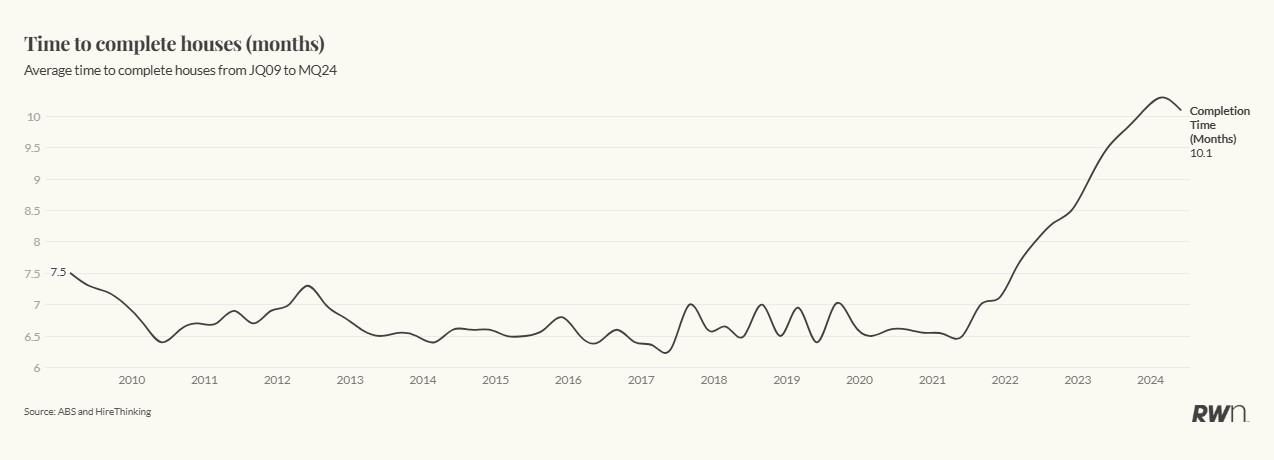
Modular construction can reduce building costs by 10-20 per cent while cutting construction timeframes by up to 50 per cent compared to traditional methods.The cost advantages stem from factory-based construction eliminating weather delays, reducing material waste through precise manufacturing, and achieving economies of scale impossible on individual construction sites. When components are manufactured in controlled environments, quality improves while labour costs decrease through more efficient deployment of skilled workers. Rather than coordinating trades across multiple sites, modular construction consolidates activities in controlled environments where workflows can be optimised, materials managed efficiently, and quality assured through standardised processes.
Right now, the use of modular in building homes is growing but not dramatically so. The market has grown from $3.7 billion in 2018 to a projected $7.7 billion by 2030, representing compound annual growth of 6.4 per cent
The future may involve even more radical innovations although widespread use is still some time away. LUYTEN’s 3D printed multi-storey home in Melbourne completed construction in just five weeks compared to the typical 8-11 months for traditional builds. Amazon’s $4,999 “snap-on” tiny home demonstrates how extreme standardisation can drive costs down dramatically.
For modular construction to achieve its potential, manufacturing capacity must expand significantly, requiring substantial investment in factory facilities. In the 2025-26 Federal Budget, the Australian Government allocated $54 million to support the prefabricated and modular housing sector. This funding comprises $49.3 million to assist state and territory programs aimed at expanding the prefab and modular housing industry, and $4.7 million to develop a voluntary national certification process to streamline approvals and uphold quality. Additionally, the government committed $120 million from the National Productivity Fund to incentivise states and territories to eliminate regulatory barriers hindering the adoption of modern construction methods, including modular and prefabricated building techniques. These initiatives are part of a broader strategy to accelerate housing construction and meet the National Housing Accord’s target of building 1.2 million new homes by 2029.